- In July, with high temperatures and busy work schedules, Yancheng Xiangsheng Carbon Fiber Technology Co., Ltd. shows its advantages in short-cut carbon fiber!
- The market size and growth of the carbon fiber industry!
- Congratulations: Hu Lijie, the general manager of Yancheng Xiangsheng Carbon Fiber Technology Co., LTD., has had his series of poems "Man in the Mist" selected for print publication and joined the documentary of the China Poetry Society!
- Congratulations: Hu Lijie, the general manager of Yancheng Xiangsheng Carbon Fiber Technology Co., LTD., has become a member of the China Chemical Writers Association!
- Carbon fiber Industry in 2025: Market Expansion from Aerospace to New Energy Vehicles!
- Yancheng Xiangsheng Carbon Fiber: Specialized in short-cutting technology, leading the way in quality carbon fiber!
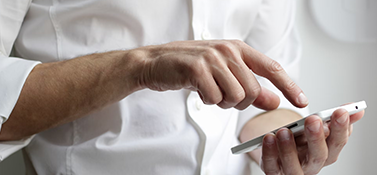
- Contact:Mr. Hu
- Cellphone:0086 - 18021868999
- Telphone:0086 - 0515-82230000
- Email:826955488@qq.com
- Address:No.1, Tonggang Road, science and Technology Park, Haitong Town, Sheyang County, Yancheng City, Jiangsu Province
Polyacrylonitrile engineering fiber
Applied to cement concrete, polyacrylonitrile fiber applied to asphalt concrete
Inquiry Now
Product Introduction
Polyacrylonitrile fiber, also known as acrylic fiber, has higher elastic modulus, tensile strength, UV resistance, and high temperature and cold resistance compared to polypropylene fiber. As the main reinforcement for cement concrete and asphalt concrete, it can significantly improve the tensile strength, fatigue strength, and flexural tensile strength of concrete, and significantly improve the early cracking resistance of concrete. Used in asphalt to significantly improve its adhesion, high-temperature stability, fatigue durability, and to prevent low-temperature cracking and reflection cracking, effectively improving tensile, shear, compressive, and impact strength. The true role and application prospects of polyacrylonitrile fibers in concrete have been recognized and accepted by the engineering community.
Application range of polyacrylonitrile fiber
Applied to cement concrete
1. Cement products such as precast concrete slabs and components
2. Cement concrete roads, pavements, bridge decks, airport runways
3. Projects in ports, deep-water docks, bridges, and severe cold areas
4. Highway anti-collision barrier and impact barrier
5. Reservoir, swimming pool, septic pool, sewage treatment pool
6. Panel dams in water conservancy and hydropower engineering
7. Waterproofing engineering for basement side walls, bottom plates, top plates, roof slabs, and other structures
8. Spraying and pumping concrete
Application of Polyacrylonitrile Fiber in Asphalt Concrete
1. New asphalt pavement surface layer
2. Old asphalt pavement overlay
3. Road surface repair
4. Cold patching and joint filling of road surface
5. Steel structure bridge deck pavement
Main functions of polyacrylonitrile fiber
When used in cement concrete:
1. Effectively improving the crack resistance of cement concrete
(1) Good adhesion with cement, supporting the aggregate, reducing bleeding and preventing settlement cracks.
(2) Adjust the water content to avoid drying shrinkage cracks caused by rapid evaporation of water.
(3) Adjust the temperature stress inside the concrete due to hydration heat release and external temperature changes, and reduce the level of cracks.
3. Reduce the brittleness of concrete and ensure the strength of cracked concrete
4. Improve the wear resistance, tensile strength, and toughness of concrete
5. Improve the impact resistance, seismic resistance, and cracking resistance of concrete
6. Greatly improving the frost resistance of concrete and effectively improving its durability
When used in asphalt concrete:
1. Improving the dispersion effect of asphalt concrete mixtures
2. Play a reinforcing role in asphalt mixtures
3. Increase the oil content of asphalt mixture, improve bonding strength and stability
4. Improving the toughness and low-temperature resistance of asphalt mixtures
5. Reduce permanent deformation and improve anti slip and wear resistance
6. Reduce the impact of temperature on asphalt pavement and improve its water stability
Main parameters of polyacrylonitrile fiber
Composition: 100% Polyacrylonitrile type bundled monofilament
Equivalent diameter 13-21um, length 6mm 10mm 19mm, according to customer requirements
Specific gravity 1.18 g/cm 3, color white or light yellow
Tensile strength ≥ 950 MPa, elongation at break 10-20%
Elastic modulus ≥ 17Gpa, good light resistance except for fluorinated fibers
Acid and alkaline resistance, good heat resistance, non melting below 220 ℃
Suggested dosage and construction process of polyacrylonitrile fiber
When used in cement concrete, generally 0.6~0.9 kg/m3
For bridge deck pavement with high impact resistance requirements, it can be between 1.5 and 1.8 kg/m3
6mm length for mortar and 10-20mm length for concrete
According to the amount of fiber added, accurately and steadily add the prepared sand, stone, and cement materials, and add a mixer to dry mix for 30 seconds, then add water to wet mix for 1 minute. The construction and maintenance of concrete after adding fibers are the same as those without fibers.
Attention: After adding fibers, the adhesion of concrete is enhanced and the slump slightly decreases. It is recommended to change the admixture and never adjust it by increasing the water consumption.
When used for asphalt concrete, the day and night traffic volume is less than 3000 1-1.5 kg/t
3000-8000 2-2 Kg/t
> 8000 3-3.5 kg/t
Used for bridge deck pavement wearing layer 3.5 kg/t
Gas film layer 2.5 kg/t
Before the aggregate is completely dry, the fibers are added together with the aggregate and mixed for more than 20 seconds. After dry mixing, asphalt is sprayed for wet mixing, with a total mixing time of no less than 60 seconds. The construction is the same as ordinary asphalt pavement, but the compaction needs to be 3-4 times more than normal compaction, with a compaction requirement of over 98%.
-
Yancheng Xiangsheng Carbon Fiber Technology Co., Ltd.
-
Mr. Hu
-
0086 - 18021868999
-
826955488@qq.com