- Short carbon fiber: the innovative choice of high-performance materials-Yancheng Xiangsheng Carbon Fiber Technology Co., LTD.
- Forecast 2025: China carbon fiber industry to maintain growth trend!
- Carbon fiber industry: Current situation, Challenges and Future Opportunities!
- Yancheng Xiangsheng Carbon Fiber Technology Co., LTD. Short-cut carbon fiber: the best choice of high-performance materials!
- Carbon fiber industry market size!
- Short carbon fiber: the innovative choice of high-performance materials-Yancheng Xiangsheng Carbon Fiber Technology Co., LTD.
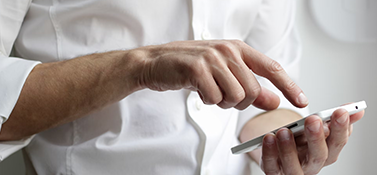
- Contact:Mr. Hu
- Cellphone:0086 - 18021868999
- Telphone:0086 - 0515-82230000
- Email:826955488@qq.com
- Address:No.1, Tonggang Road, science and Technology Park, Haitong Town, Sheyang County, Yancheng City, Jiangsu Province
Japan's new energy and industrial technology
Release date: [2017/2/23]
Read total of [802] times
Japan's new energy and industrial technology development organization (NEDO) and the University of Tokyo, Japan Industrial Technology Research Institute, Toray, through joint research, developed a production efficiency increased to 10 times the current production process of carbon fiber (CF) manufacturing methods. Is characterized by the need for 30 to 60 minutes of the sintering time is shortened to about 5 minutes.
In order to meet the increasingly stringent global fuel efficiency regulations, to high-end car as the center, automotive body using CFRP (carbon fiber reinforced resin-based composite materials) more and more. However, the global supply of PAN (polyacrylonitrile) carbon fibers for this material is only about 50,000 tonnes in 2014. In order to use CFRP on the production vehicle in the future, it is necessary to increase the production of PAN carbon fiber and reduce the manufacturing cost.
At present, the global PAN class carbon fiber manufacturers use is called "into the way" manufacturing methods. This is the technology invented in 1959, Toray, Teijin, Mitsubishi Rayon and other Japanese manufacturers are also using the technology based on the manufacture of carbon fiber (Figure 1).
\
Figure 1: Current PAN-based carbon fiber manufacturing method
PAN is spun into the wire after the implementation of refractory treatment, that is, the air heated to 200 ~ 300 ℃ to oxidation, to give its heat resistance. The process takes 30 to 60 minutes.
The method of making the method is to first mix the solvent and the catalyst in the PAN copolymer, and then spin it up and roll it up. Next to the "fire treatment", is to roll up the PAN fiber wire into the furnace to oxidize, to give its heat resistance. Heating temperature of 200 ~ 300 ℃, heating time takes 30 to 60 minutes. After the refractory treatment, the PAN fiber is heated in an additional heating furnace to 1000 to 2000 ° C to be carbonized to produce carbon fiber. The carbonation treatment takes only a few minutes.
Although the global carbon fiber manufacturers long-term use of the way, but this way more time-consuming refractory treatment, the "small tow" (by 12,000 fiber twisted carbon fiber), the production line of each line limit Is about 2,000 tons. And from the equipment cost point of view, each production line needs 10 billion to 20 billion yen as much. This is the biggest reason why carbon fiber is expensive. The current price of carbon fiber per kilogram is around 3,000 yen. To use CFRP on a production vehicle, it is necessary to increase the productivity of carbon fiber, reduce manufacturing costs, and reduce the price to less than 1,000 yen.
Eliminating the need for refractory treatment
To this end, NEDO in 2011 launched the "innovative new construction materials research and development" national projects, the goal is to save the production efficiency to prevent the improvement of refractory treatment. Tokyo University, Tokyo, Japan, Lai Sun, participated in the project, and was dedicated to the development of new manufacturing methods (Figure 2) under the five-year plan for the year 2015.
\
Figure 2: Manufacturing technology developed by the University of Tokyo
By making the oxidation treatment in the liquid rather than the original refractory treatment, the spinning process can be shortened to about 5 minutes.
In the manufacturing method led by the University of Tokyo, a new type of polymer (precursor polymer) was developed to remove refractory treatment. The essential point is that the polymer is spun into the filament and does not undergo the original refractory treatment but is oxidized in the solvent.
And then carbonized by heating with a microwave heating device to 1000 ° C or higher. Heating time only 2 to 3 minutes. After the carbonization treatment, the plasma is subjected to surface treatment to produce carbon fibers. The plasma treatment takes less than 2 minutes. In this way, the original need 30 to 60 minutes of sintering time can be shortened to about 5 minutes. In the novel manufacturing method, the plasma treatment is carried out in order to improve the bonding between the carbon fiber and the thermoplastic resin as the CFRP base material.
Use low cost clothing for PAN
The polymer as a raw material is not a PAN copolymer for the current carbon fiber, but a low-cost PAN material for clothing. Add an oxidizing agent to the PAN for clothing and dissolve it in a solvent to oxidize in a short period of time. Since it is oxidized in the liquid, it is also necessary to add a solubilizing accelerator. The previous step of carbonization treatment using microwave is the same as that of the conventional propylene fiber manufacturing process (Fig. 3).
\
Figure 3: Manufacture of carbon fibers with new processes
(A) a precursor polymer produced using a low price PAN for clothing. (B) adding a dissolution accelerator and an oxidizing agent to the spun yarn, and performing an oxidation treatment in the liquid. (C) Carbon fibers made with new processes.
The carbon fiber produced by the new manufacturing method had a tensile modulus of 240 GPa, a tensile strength of 3.5 GPa and an elongation of 1.5%. These values are the same level as the Toray GM grade carbon fiber "T-300" used for sporting goods.
The future issue is to include the pre-process, and to shorten the time of mass production throughout the manufacturing process. In order to improve the production efficiency and increase the amount of PAN fiber (improve the "fineness") in the refractory treatment of the conventional manufacturing method, the difficulty of controlling the oxidation reaction is increased and the sintering speed can not be increased. The fineness of the filament is expressed in terms of the weight of the fiber length per meter.
And the new manufacturing method in the liquid oxidation treatment, rather than the implementation of refractory treatment, it can easily improve the PAN fiber fineness, can be a lot of treatment. Further, the new method is a carbonization treatment using a microwave heating apparatus, so that the sintering time is greatly shortened.
"With the improvement of fineness and the shortening of sintering time, even if the production level, the production efficiency can be increased to the current 10 times."
In order to meet the increasingly stringent global fuel efficiency regulations, to high-end car as the center, automotive body using CFRP (carbon fiber reinforced resin-based composite materials) more and more. However, the global supply of PAN (polyacrylonitrile) carbon fibers for this material is only about 50,000 tonnes in 2014. In order to use CFRP on the production vehicle in the future, it is necessary to increase the production of PAN carbon fiber and reduce the manufacturing cost.
At present, the global PAN class carbon fiber manufacturers use is called "into the way" manufacturing methods. This is the technology invented in 1959, Toray, Teijin, Mitsubishi Rayon and other Japanese manufacturers are also using the technology based on the manufacture of carbon fiber (Figure 1).
\
Figure 1: Current PAN-based carbon fiber manufacturing method
PAN is spun into the wire after the implementation of refractory treatment, that is, the air heated to 200 ~ 300 ℃ to oxidation, to give its heat resistance. The process takes 30 to 60 minutes.
The method of making the method is to first mix the solvent and the catalyst in the PAN copolymer, and then spin it up and roll it up. Next to the "fire treatment", is to roll up the PAN fiber wire into the furnace to oxidize, to give its heat resistance. Heating temperature of 200 ~ 300 ℃, heating time takes 30 to 60 minutes. After the refractory treatment, the PAN fiber is heated in an additional heating furnace to 1000 to 2000 ° C to be carbonized to produce carbon fiber. The carbonation treatment takes only a few minutes.
Although the global carbon fiber manufacturers long-term use of the way, but this way more time-consuming refractory treatment, the "small tow" (by 12,000 fiber twisted carbon fiber), the production line of each line limit Is about 2,000 tons. And from the equipment cost point of view, each production line needs 10 billion to 20 billion yen as much. This is the biggest reason why carbon fiber is expensive. The current price of carbon fiber per kilogram is around 3,000 yen. To use CFRP on a production vehicle, it is necessary to increase the productivity of carbon fiber, reduce manufacturing costs, and reduce the price to less than 1,000 yen.
Eliminating the need for refractory treatment
To this end, NEDO in 2011 launched the "innovative new construction materials research and development" national projects, the goal is to save the production efficiency to prevent the improvement of refractory treatment. Tokyo University, Tokyo, Japan, Lai Sun, participated in the project, and was dedicated to the development of new manufacturing methods (Figure 2) under the five-year plan for the year 2015.
\
Figure 2: Manufacturing technology developed by the University of Tokyo
By making the oxidation treatment in the liquid rather than the original refractory treatment, the spinning process can be shortened to about 5 minutes.
In the manufacturing method led by the University of Tokyo, a new type of polymer (precursor polymer) was developed to remove refractory treatment. The essential point is that the polymer is spun into the filament and does not undergo the original refractory treatment but is oxidized in the solvent.
And then carbonized by heating with a microwave heating device to 1000 ° C or higher. Heating time only 2 to 3 minutes. After the carbonization treatment, the plasma is subjected to surface treatment to produce carbon fibers. The plasma treatment takes less than 2 minutes. In this way, the original need 30 to 60 minutes of sintering time can be shortened to about 5 minutes. In the novel manufacturing method, the plasma treatment is carried out in order to improve the bonding between the carbon fiber and the thermoplastic resin as the CFRP base material.
Use low cost clothing for PAN
The polymer as a raw material is not a PAN copolymer for the current carbon fiber, but a low-cost PAN material for clothing. Add an oxidizing agent to the PAN for clothing and dissolve it in a solvent to oxidize in a short period of time. Since it is oxidized in the liquid, it is also necessary to add a solubilizing accelerator. The previous step of carbonization treatment using microwave is the same as that of the conventional propylene fiber manufacturing process (Fig. 3).
\
Figure 3: Manufacture of carbon fibers with new processes
(A) a precursor polymer produced using a low price PAN for clothing. (B) adding a dissolution accelerator and an oxidizing agent to the spun yarn, and performing an oxidation treatment in the liquid. (C) Carbon fibers made with new processes.
The carbon fiber produced by the new manufacturing method had a tensile modulus of 240 GPa, a tensile strength of 3.5 GPa and an elongation of 1.5%. These values are the same level as the Toray GM grade carbon fiber "T-300" used for sporting goods.
The future issue is to include the pre-process, and to shorten the time of mass production throughout the manufacturing process. In order to improve the production efficiency and increase the amount of PAN fiber (improve the "fineness") in the refractory treatment of the conventional manufacturing method, the difficulty of controlling the oxidation reaction is increased and the sintering speed can not be increased. The fineness of the filament is expressed in terms of the weight of the fiber length per meter.
And the new manufacturing method in the liquid oxidation treatment, rather than the implementation of refractory treatment, it can easily improve the PAN fiber fineness, can be a lot of treatment. Further, the new method is a carbonization treatment using a microwave heating apparatus, so that the sintering time is greatly shortened.
"With the improvement of fineness and the shortening of sintering time, even if the production level, the production efficiency can be increased to the current 10 times."
Lastest News
- Short carbon fiber: the innovative choice of high-performance materials-Yancheng Xiangshen
- Forecast 2025: China carbon fiber industry to maintain growth trend!
- Yancheng Xiangsheng Carbon Fiber Technology Co., LTD. Short-cut carbon fiber: the best cho
- Carbon fiber industry: Current situation, Challenges and Future Opportunities!
- Short carbon fiber: the innovative choice of high-performance materials-Yancheng Xiangshen
- Carbon fiber industry market size!