- The summer solstice has passed. Yancheng Xiangsheng Carbon Fiber Technology Co., Ltd. showcases the outstanding performance and diverse applications of its chopped carbon fibers!
- Forecast of the Future Development Trend of the Carbon Fiber Industry!
- On the summer solstice, explore the mystery of short-cut carbon fiber at Yancheng Xiangsheng Carbon Fiber Technology Co., LTD.!
- Yancheng Xiangsheng Carbon Fiber Technology Co., LTD. Chopped Carbon Fiber: The Key to Innovation in high-performance Materials!
- In 2024, the production capacity of China's carbon fiber industry will continue to grow at a relatively fast pace!
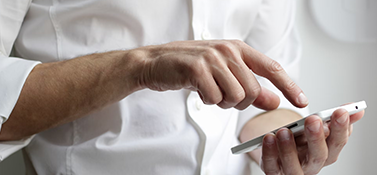
- Contact:Mr. Hu
- Cellphone:0086 - 18021868999
- Telphone:0086 - 0515-82230000
- Email:826955488@qq.com
- Address:No.1, Tonggang Road, science and Technology Park, Haitong Town, Sheyang County, Yancheng City, Jiangsu Province
The specific use of carbon fiber powder!
The use of carbon fiber powder will vary depending on the application field, the following are some examples of common areas of use:
Composite material field:
Choose the right base material: such as resin (epoxy resin, unsaturated polyester resin, etc.), plastic (polyethylene, polypropylene, etc.), metal (aluminum, magnesium, etc.) or rubber. According to the specific performance requirements and application scenarios, select the matrix material with good compatibility with carbon fiber powder.
Surface treatment: Appropriate surface treatment of carbon fiber powder to improve its binding force with the matrix. For example, chemical treatment (such as acid treatment, coupling agent treatment) or physical treatment (such as plasma treatment, ultraviolet irradiation) is used to increase the surface activity and roughness of carbon fiber powder.
Mixing and dispersion: the carbon fiber powder is evenly mixed with the base material. Mechanical stirring, ultrasonic dispersion, and three-roll grinding can be used to ensure that the carbon fiber powder is evenly dispersed in the matrix to avoid agglomeration. For example, when making carbon fiber reinforced resin composites, the resin matrix is first mixed with an appropriate amount of curing agent, and then the carbon fiber powder is gradually added during the mixing process, and the mixing is continued until the mixture is uniform.
Molding process: According to the final shape and requirements of the composite material, choose the appropriate molding process, such as injection molding, die molding, extrusion molding, winding molding, etc. In the molding process, the process parameters (such as temperature, pressure, time, etc.) should be controlled to ensure the performance and quality of the composite material. For example, when manufacturing carbon fiber reinforced plastic parts, the injection molding process is used, and the mixed material is injected into the mold and solidified under a certain temperature and pressure.
Battery material field:
Formula design: Determine the composition and proportion of positive and negative electrode materials of the battery, and add carbon fiber powder as a conductive additive. At the same time, consider the selection and dosage of other additives (such as binders, active substances, etc.) to optimize the performance of the battery.
Mixing: The carbon fiber powder is thoroughly mixed with other components of the positive and negative electrode material. Equipment such as planetary agitators and high-speed dispersors can be used to stir for a long time in the presence of appropriate solvents (such as N-methylpyrrolidone, water, etc.) to ensure that the components are evenly dispersed.
Coating and drying: the mixed slurry is evenly coated on the fluid collector (such as copper foil, aluminum foil), and then dried to remove the solvent and obtain the electrode sheet. The coating method can be scraper coating, spraying, dipping, etc. For example, in the preparation of positive electrode materials for lithium-ion batteries, a positive electrode slurry containing carbon fiber powder is coated on aluminum foil and dried at a certain temperature to form a positive electrode sheet.
Battery assembly: The prepared positive and negative electrode sheet, diaphragm, electrolyte, etc. are assembled into a battery. According to the battery type and design requirements, packaging, welding and other operations to complete the battery assembly.
Electronic field:
Conductive coatings and inks: carbon fiber powder are added to the formulation of conductive coatings or inks to improve their conductive properties. In the preparation process, attention should be paid to controlling the content and dispersion of carbon fiber powder, as well as the viscosity of paint or ink, drying speed and other performance indicators. For example, when making conductive ink, carbon fiber powder is mixed with resin, solvent, auxiliary agent, etc., after grinding, dispersion and other processes, conductive ink is obtained, which can be used for printed electronic lines, electromagnetic shielding coating, etc.
Electronic chip packaging: Adding carbon fiber powder to the packaging material of the electronic chip can enhance the strength, thermal conductivity and electrical conductivity of the packaging material. The specific method is to mix carbon fiber powder with packaging resin and carry out injection molding or potting and other processes to realize the package protection of the chip.
Conductive rubber and plastic: For the manufacture of conductive rubber or plastic parts, carbon fiber powder is mixed with a rubber or plastic matrix. Through the appropriate processing technology (such as mixing, extrusion, injection molding, etc.), the carbon fiber powder forms a conductive network in the matrix, giving the material conductive properties. For example, when producing conductive rubber keys, carbon fiber powder is mixed into the rubber material and the conductive rubber keys are formed and processed.
Yancheng Xiangsheng Carbon Fiber Technology Co., Ltd. Registered trademark "Xiangli", is committed to the research of carbon fiber, aramid fiber and other special fiber composite materials functionality and design diversity, It has developed 16 series products with independent intellectual property rights, such as rotorcraft shell, landing gear, aircraft plant protection spray system, seaplane float, swamp boat, aerodynamic boat, aviation communication helmet, carbon fiber for plastic reinforcement, carbon fiber powder for friction materials, short carbon fiber for braking system, as well as carbon fiber rope, carbon fiber cloth, carbon fiber filament special fiber cutting machine.
- The summer solstice has passed. Yancheng Xiangsheng Carbon Fiber Technology Co., Ltd. show
- Forecast of the Future Development Trend of the Carbon Fiber Industry!
- On the summer solstice, explore the mystery of short-cut carbon fiber at Yancheng Xiangshe
- Yancheng Xiangsheng Carbon Fiber Technology Co., LTD. Chopped Carbon Fiber: The Key to Inn
- In 2024, the production capacity of China's carbon fiber industry will continue to grow at
- Chopped carbon fiber: The core force of the lightweight revolution!